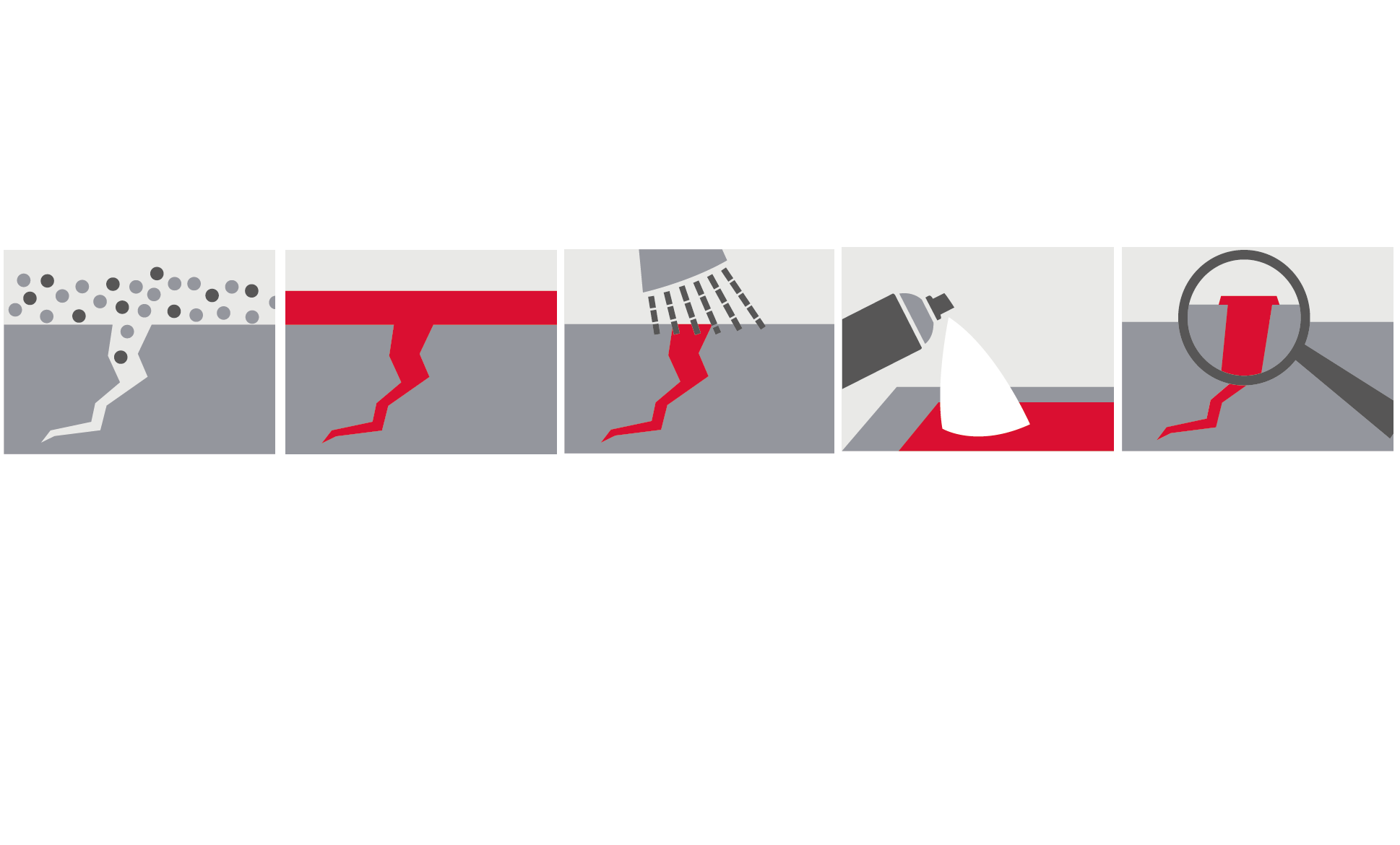
HOW TO DO DYE PENETRANT (LPI) TESTING?
Liquid Penetrant (DPI-LPI) is a Non-Destructive Testing (NDT) method to inspect discontinuities that are open to the surface. In this method, special dyestuffs (penetrants) that can penetrate the discontinuity with the principle of the capillary are used. You can find the application steps of liquid penetrant inspection below.
- Surface Preparation and Pre-Cleaning
One of the most important points to be considered in the liquid penetrant application is that the discontinuity must be open to the surface. If the discontinuity open to the surface is closed due to oil, dirt, dust, etc., or if there is any factor that will prevent the penetrant liquid penetrates into discontinuity, the area to be tested must be free of these factors.
Before the application, the test area must be cleaned with suitable pre-cleaners. In some cases, mechanical cleaning such as sandblasting, sandpapering, cleaning the surface with a brush, ultrasonic cleaning may also be required just before this process. The surface must be thoroughly dried before applying penetrant liquid to the surface.
- Application of the Penetrant Liquid
It is the step in which liquid penetrant is applied to the test area. Penetrant spraying on the surface is the most preferred method, dipping the test piece in penetrant liquid or applying liquid penetrant to the surface with a brush is preferred as well. The penetrant should be applied uniformly to the surface.
- Dwelling Time
Depending on the type of penetrant used, the geometry of the test part, and temperature conditions, a dwelling time of 5-60 minutes is required for the penetrant liquid penetrates into discontinuity. If there is too short a dwell time, there will not be enough penetration. If the dwelling time is too long, the penetrant liquid will dry on the surface. Ideal dwelling time should be determined as the optimum as a result of the manufacturer's recommendations and the experiments to be carried out by the applicator.
- Excess Penetrant Removal
For easier detection of discontinuities, the excess penetrant liquid that does not penetrate into the discontinuity should be removed from the surface.
According to penetrant type and the application method; the excess penetrant removal process can be done by rinsing with water, or excess penetrant can be wiped from the surface with a lint-free rag in the presence of a solvent. In some application methods, emulsifiers are also used to rinse excess penetrant liquid from the surface with water.
Excess penetrant cleaning is the most critical step of the dye penetrant application. The penetrant liquid that is into discontinuity will also be removed as a result of too much cleaning to be carried out more than necessary. If the method of rinsing with water is preferred; The water pressure should not be high enough to remove the penetrant in the discontinuity. In the method of cleaning with a rag; Excess penetrant should be wiped off the surface with only one-way directions (like only from top to bottom or only from left to right). In applications with solvent, the solvent should be applied to the rag, not directly to the surface.
- Developer Application
To determine the location and type of the discontinuity; The penetrant in the discontinuity must somehow rise to the surface. For this purpose, developers are applied to the surface, usually in white color, which can raise the penetrant to the surface in order to ensure distinguishability. Aerosol and dry powder forms are mostly preferred.
Depending on the type of penetrant and developer used, geometry of the test part, and temperature conditions, a developer dwelling time of 10 to 60 minutes is required. Ideal developer dwelling time should be determined as the optimum as a result of the manufacturer's recommendations and the experiments to be carried out by the user.
- Inspection
Evaluation of the findings should be done under the appropriate lighting conditions specified in the relevant standards. The test piece must be evaluated within the time period written in the test procedure. The size of a discontinuity can grow over time as the penetrant raise out to the surface, causing an acceptable discontinuity to become a rejectable defect.