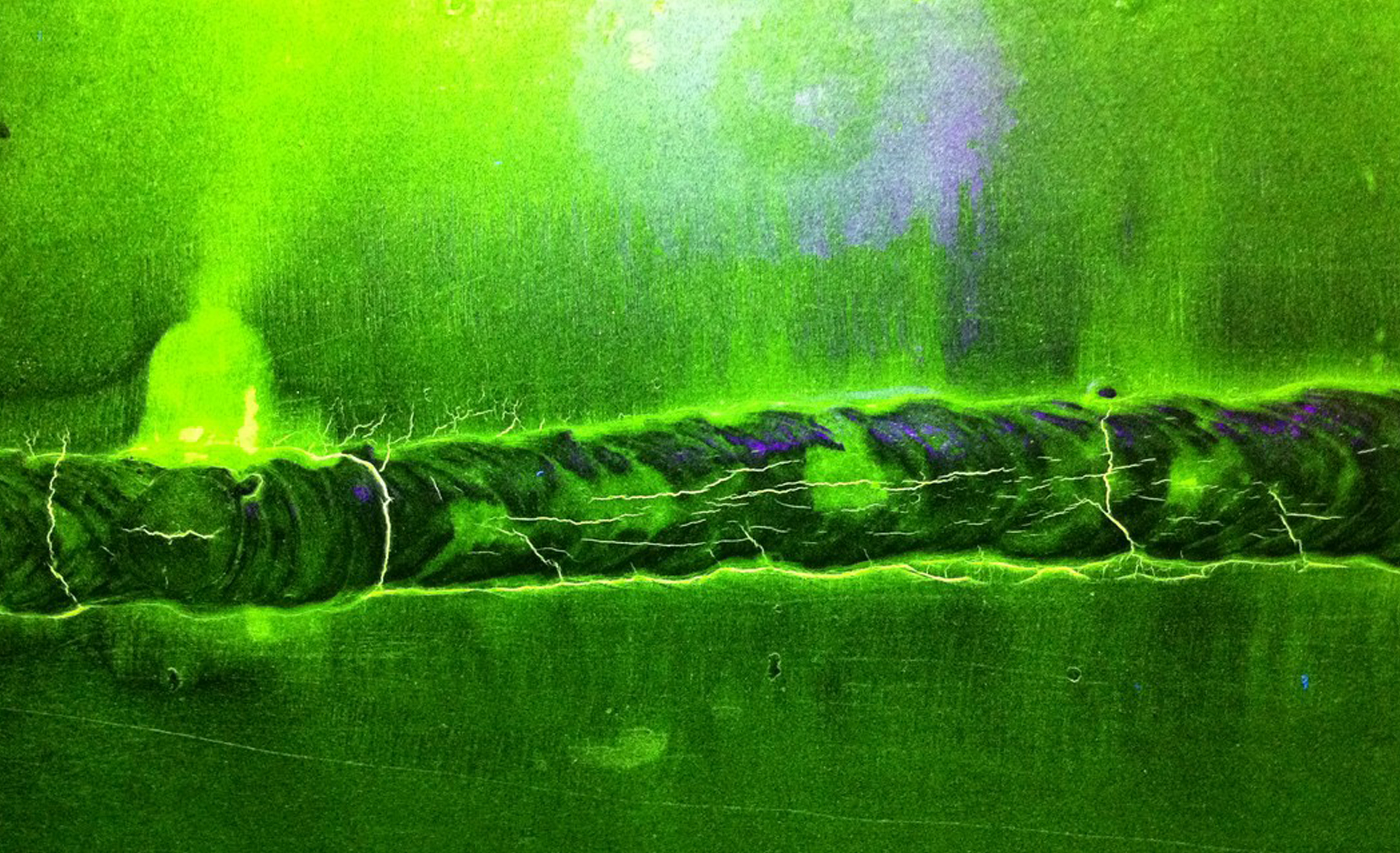
WHAT IS THE MAGNETIC TEST
Magnetic Particle Method
The History of the Method:
The history of the Magnetic Particle Method date back about 150 years. In the 1870s, it was observed that discontinuities on the surface create leakage flux with a permanent magnet. Since the knowledge about electro-physics was not sufficient in these years, the basic steps regarding this method were taken with the patent obtained by William Hooke in 1922. William Hooke discovered that he could use metallic shavings to create patterns on a magnetized ferromagnetic surface. These patterns cluster around the location of surface defects and indicate their location, just as magnetic particles are used to identify defects today. In the 1930s, the railroad industry began using Hooke's findings to study ferromagnetic materials, and the method soon became the standard way to identify defects in materials. Then, based on this information, studies were developed for the detection of discontinuities on the surface of ferromagnetic materials by magnetic methods.
The Basis of the Method:
Magnetic particle inspection (often abbreviated as MT or MPI) is a non-destructive testing (NDT) method that detects defects at or very close to the surface of ferromagnetic materials. Magnetic Particle Inspection (MPI MT) detects cracks, pores, shrinkage voids, gas voids, etc. in magnetic materials. It is a very effective method for detecting surface and light subsurface defects.
The basis of the magnetic particle inspection method; It is the formation of stray magnetic flux in the discontinuities on the material surface by the magnetization of the inspection piece, the collection of iron powders sprayed on the material surface on the discontinuities. By examining the indications formed in this way, an evaluation is made for surface defects.
The main application steps of the magnetic particle method are as follows;
1. Pre-cleaning on the inspection surface
2. Demagnetization if needed
3. Application of magnetizing current
4. Spraying of ferromagnetic powders (usually simultaneously with the application phase of the magnetizing current)
5. Interruption of the magnetizing current
6. Review
7. Evaluation and report preparation
8. Demagnetization and final cleaning